Manufacturing Procedures
2021-03-18
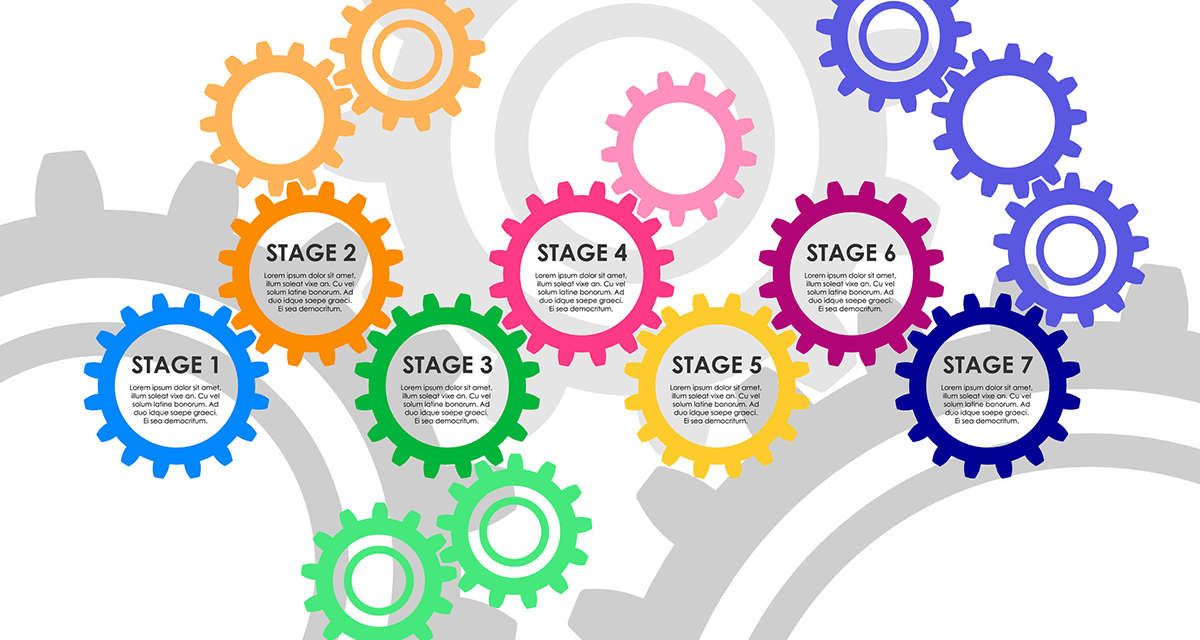
Gear parts production process
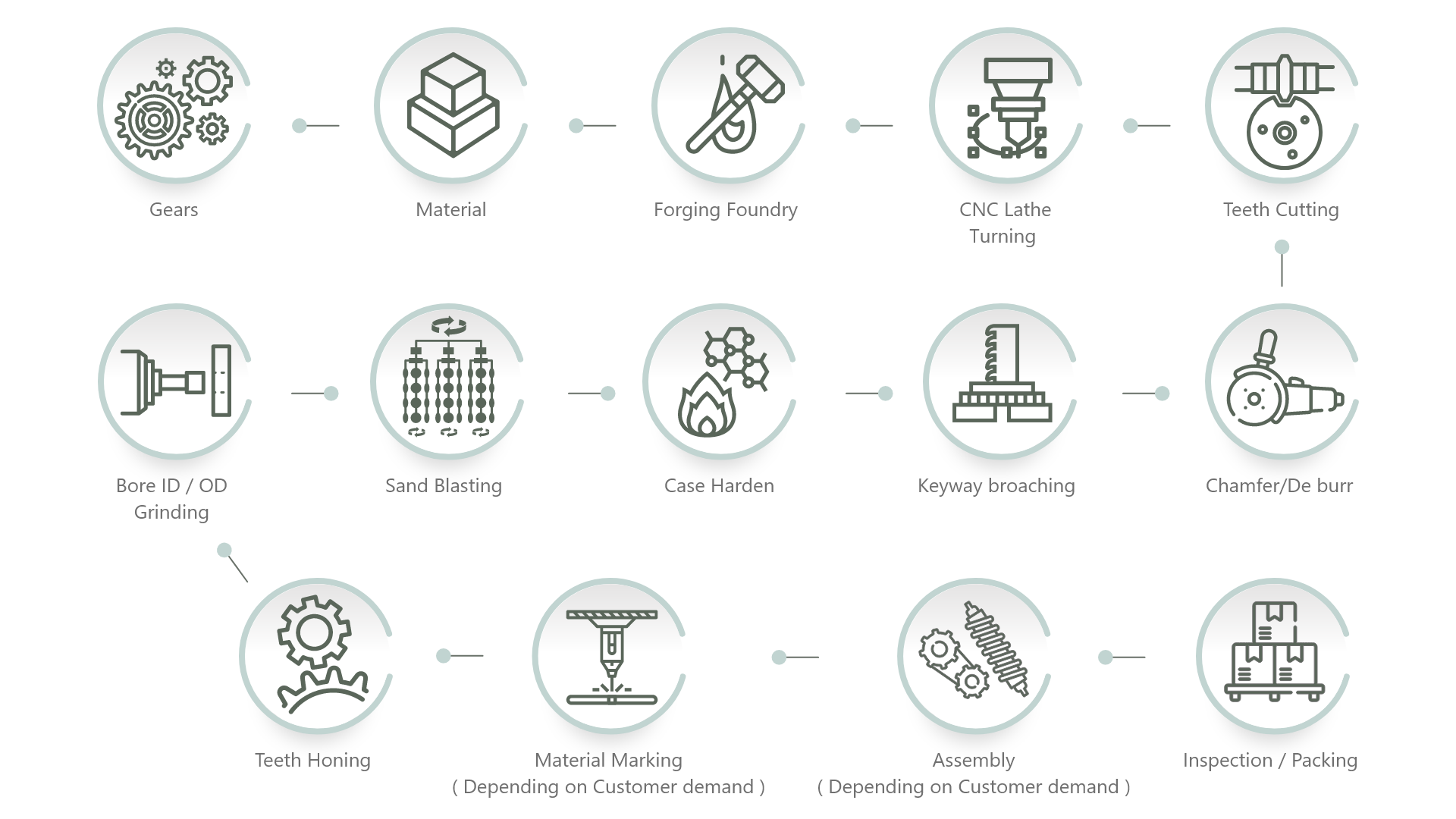
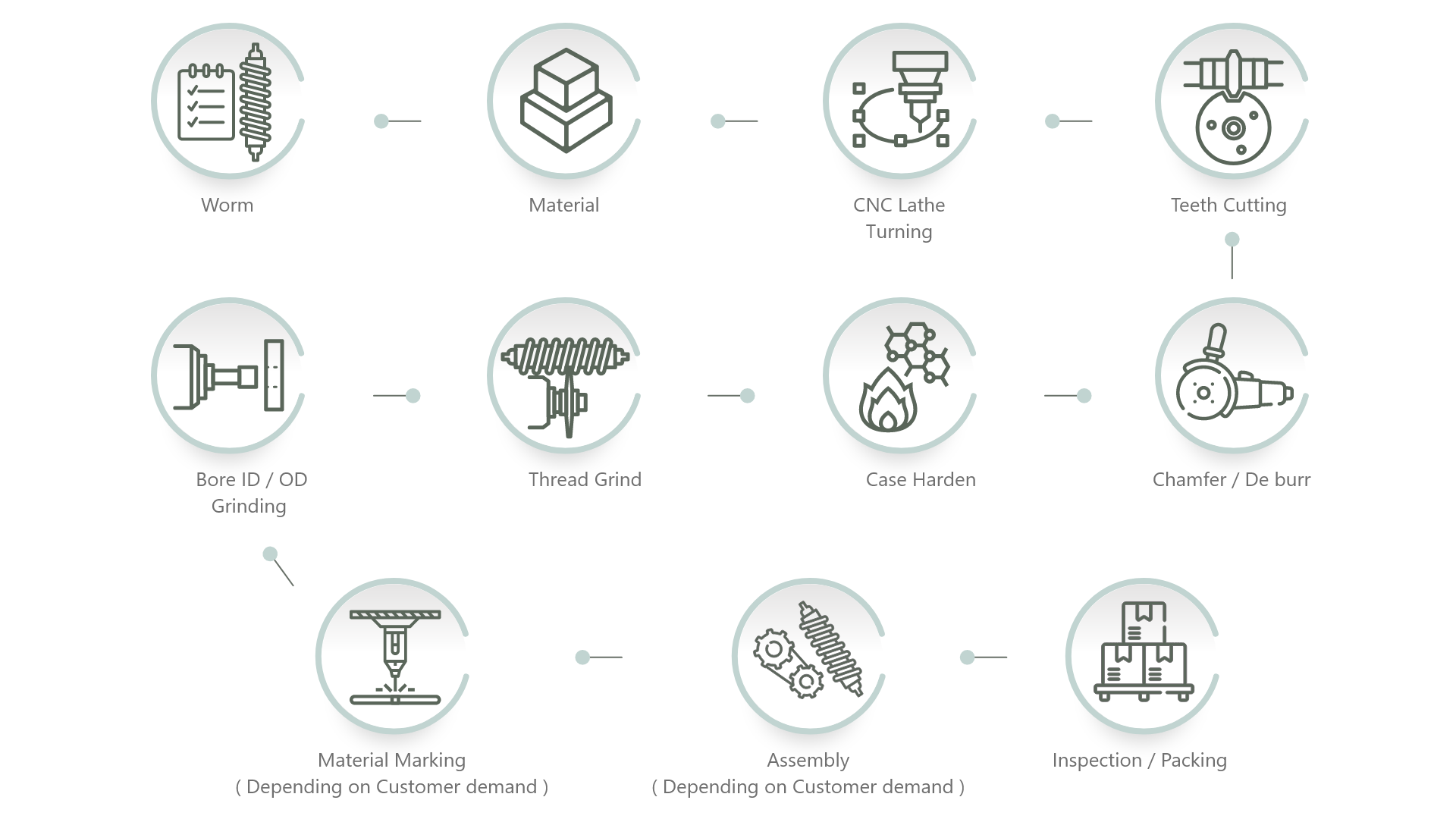
Die casting production process
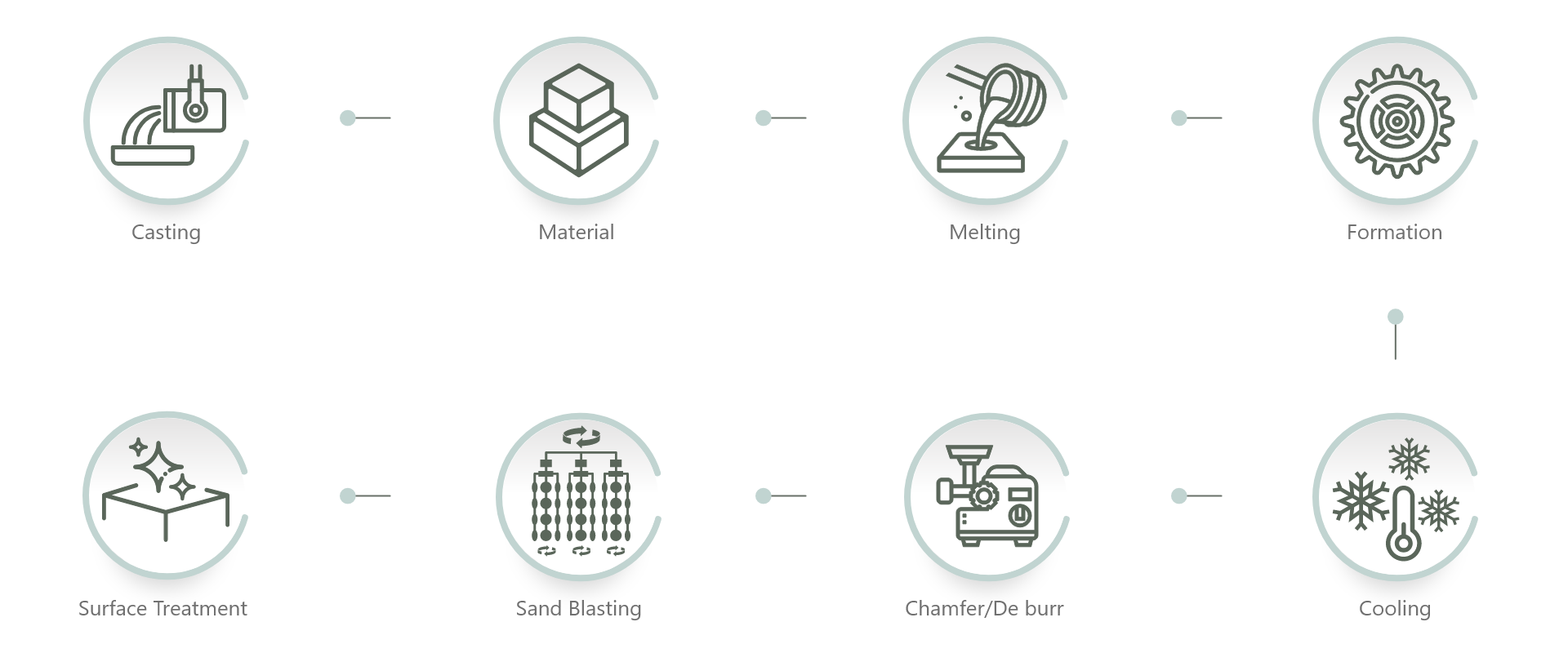
Precision machining production process
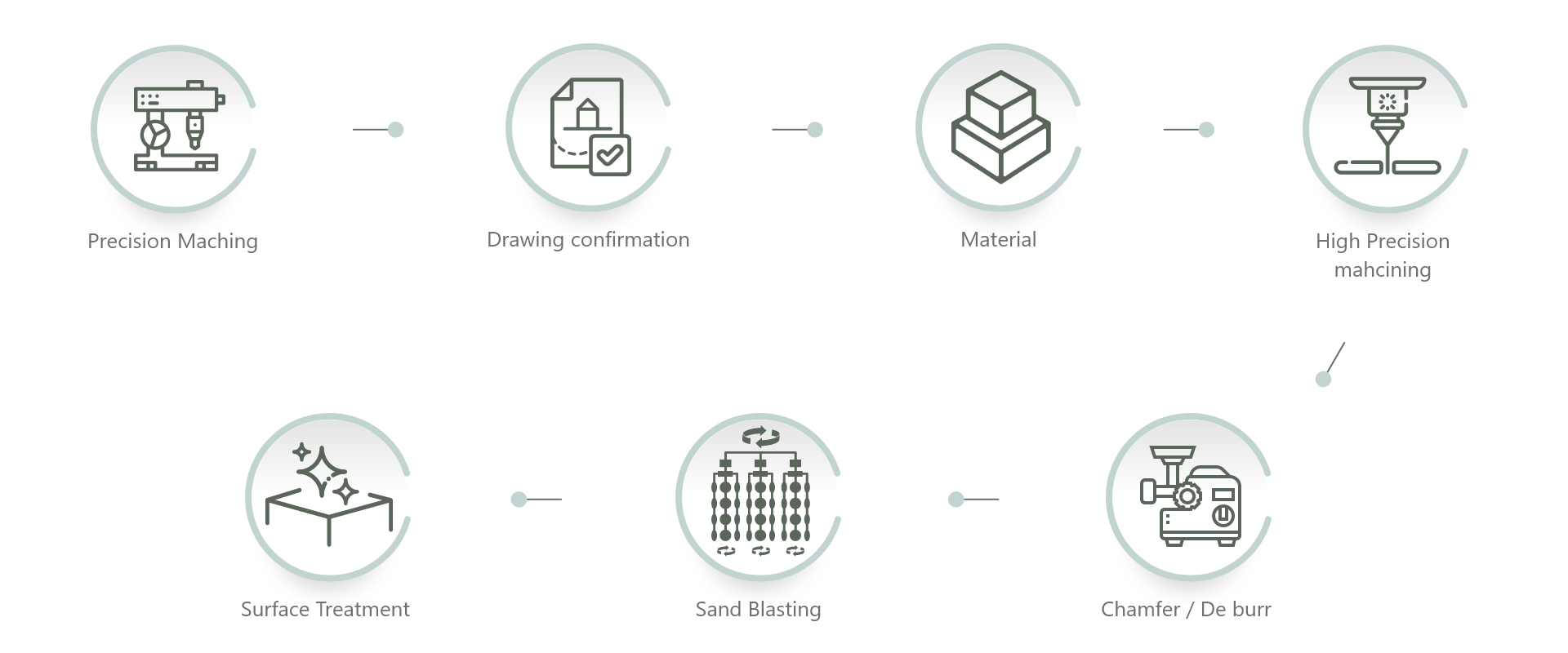
Manufacturing Procedures of Worm & Worm Gear
Process of Worm
- Step 1. Material
Using the correct material for worms is very important, this is related to the running life of the whole worm wheel set, as well as the result of the case harden process. - Step 2. CNC Lathe Turning
Controlling the outside diameter tolerance strictly on this step will enhance the following worm thread procedure. - Step 3. Worm Thread Rolling Cutting
The worm can be made from different processes such as rolling cutting, general blade cut, and even plunge grinding. Orris can make any kind of worm that fits customers’ requirements. The main manufacturing method is rolling cutting by on-shelf or be-spoke hob tools. The hob design is very important which decide the flank form and efficiency. - Step 4. Case Harden
A good quality worm wheelset with stable working performance may decide from the hardness of worm and worm wheel, a soft wheel mating to a hardened worm will conduct a good running life of worm wheelset. - Step 5. Worm Thread Grind
The grinding process could level up the grade of the worm wheelset and increase the efficiency when working. - Step 6. Bore ID Grinding
According to the mating parts' request to go through ID bore grinding. - Step 7. Inspection and Rolling Test
An accurate Worm Profile/Lead inspection report is the most important to prove that the worm is in the good quality grade and make sure the production batch is the same quality. Orris not only makes production but also uses KLINGELNBERG P26 for inspection.
Process of Worm Gear
- Step 1. Material
Normally choose Phosphor Bronze that is made from solid bar or forging, sometimes use POM/Delrin to make the plastic wheel. The material chosen comes from the application of the worm gear use. - Step 2. CNC Lathe Turning
Controlling both outside diameter and ID bore tolerance strictly on this step will enhance the following worm gear cutting. - Step 3. Keyway Milling/Broaching
Orris has our own keyway broaching machine and machining in-house which could control the tolerance well. - Step 4. Teeth Cutting
The Module detail, ratio and worm flank, etc. of the hobbing tool is very important to cut high-quality teeth on the worm gear, Orris has the ability to design the hob gear data that match our cutting machine and the performance appearance from customers. - Step 5. Chamfer/De burr
Orris has a Chamfering Machine from Japan that could process the chamfer automatically. A clean surface is the basic supply term for all of the finished products from Orris Drive. - Step 6. Inspection and Rolling Test
An accurate Worm Gear Profile/Lead inspection report is the most important to prove that the worm gear in the good quality grade and make sure the production batch is the same quality. Orris not only makes production but also uses KLINGELNBERG P26 for inspection.